When discussing forge welding, often generalized as Electric Resistance Welding (ERW), the critical agents of a successful process are heat and forge pressure. Throughout the years, generating the heat portion of the equation has moved from black magic to a highly specialized science thanks to class-leading companies such as Thermatool Corporation, EFD Induction, and Emmedi. The type of welding apparatus, along with the weld squeeze box, form a synergy and rely on each other to become successful.
ERW can typically be broken down into three (3) main types of welding: rotary electrode or contact at medium to low frequency, high frequency (HF) contact, or high frequency (HF) induction.
Rotary Electrode or Contact (Medium to Low Frequency)
Pertains to a very mature edge heating method that literally involves a rotating copper electrode coupled with a bottom squeezebox setup as an integral assembly (see Figure 1). Figure 1
This technology is very robust and can be used on very small diameters in the world of today. Many years ago, it was the dominant welding form for all diameter. Setting up this system was less complicated than the HF weld methods but had its own downsides which included limited materials applications, initial and operating expenses, along with limited size applications. Its strengths were focused on the simplicity of weld setup and the robustness of inadequate setups still yielding a good product.
HF Contact
As mentioned earlier, a rotary electrode is a contact form of welding, but another contact form is via stationary copper contacts powered by a high frequency (HF) power supply. These copper contacts ride along the weld vee and are positioned within the process flow just before the weld squeeze box (see Figure 2).
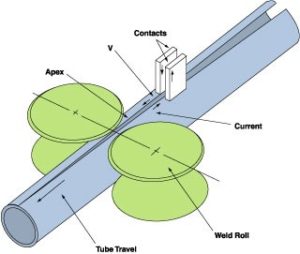
Image courtesy of The Fabricator, The Tube & Pipe Journal, June 2002. Article “Electric resistance welding at a glance” written by Gerald Weimer & Ray Cagganello.
HF Contact welding has really become only viable towards large diameter, very thick wall pipe applications. Even then, this market is being eroded by HF Induction. This is due to the constant consumable cost of the stationary contact electrodes. This is a downside to this process but truth be told, it is very efficient for heavy wall applications.
HF Induction
Spawned with the same type of power supply, HF Induction has truly become the dominant form of welding for the tube market (carbon steels, copper, and aluminum) (see Figure 3).
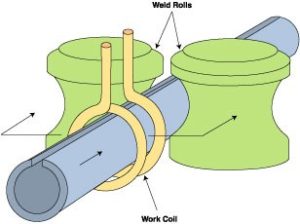
Image courtesy of The Fabricator, The Tube & Pipe Journal, June 2002. Article “Electric resistance welding at a glance” written by Gerald Weimer & Ray Cagganello.
In the last thirty years, companies such as Thermatool Corporation, EFD Induction, Emmedi, and many others have bridged this gap from “black art” to a truly scientific solution for welding. One might naturally think that the heating portion would be the most difficult, and for many years, it was the dominant variable in the welding success equation. The other half (often referred to as the mechanical portion) is often dumbed down as “easy” even though it has certain nuisances it must overcome.
First, the squeeze assembly, which applies forging pressure, must be RIGID. The minimal amount of flex in the system typically results in the best, most consistent welds. Applying this pressure in the right locations can be difficult to do. Essentially, it’s a balancing act in 3-D space…you have a product, optimal setup of the electrical welding parameters which affect electrical coupling efficiency which dictates many aspects of the weld zone area and the need for strength. These parameters will often dictate the right weld squeeze box for you.
This chart is generalized and there are always exceptions that might push you to an alternative.
Finally, if you are interested in the aforementioned electrical welding parameters which affect electrical coupling efficiency concepts, I recommend reading Chapters 4 and 9 of High Frequency Pipe & Tube Welding 1st Edition 1994/1995 compiled and edited by Robert K. Nichols, P.E. formerly from Thermatool Corporation. In this reading, you will gain the mathematical derivations which will ultimately lead you to the chart generalizations as shown above.