Machine Effects on a Formed Section
Roll forming machines, like most metalworking or forming equipment, are available in a range of sizes. A roll forming machine with more passes can produce a more complex shape, as each successive pass of the machine is able to form additional bends to produce the desired profile. In addition to the complexity of the profile, the overall size of profile that can be roll formed on a specific machine is dependent on several machine specifications.
The most straightforward is roll space. The roll space, or the area on each pass where the roll tooling is loaded, is the limiting factor for the width of the metal strip that can be roll formed. For example, a machine with 18 in. roll space cannot form a strip wider than 18 in. When the flat strip comes into the machine, that is the point where the greatest roll space is required. As the bends are progressively formed into the strip, the overall width requirement of the machine decreases.
The capability of any given machine with regard to height or depth of the section is measured mainly by the vertical distance available between spindles. This, together with the distance from the center-line of the bottom spindle to the top of the machine base and the horizontal center distance between roll stands, establishes the maximum roll diameter.
Let us look at the roll contour of the last roll stage for a simple channel as on Figure #1 and note its relation to the other parts of the machine.
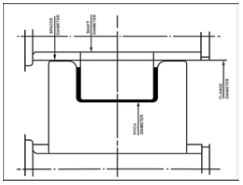
In addition to the restrictions just mentioned, there must be clearance between the outside diameter of the bottom roll flange and the top roll spacer, as well as clearance between the edge of the section and the top roll spacer. Note also the bottom roll flange diameter includes a lead-in or bell-mouthed contour to aid in threading from one pass to another.
Roll Pitch Diameter and Gearing Ratio
The roll “pitch” diameter is usually selected to engage a given profile at its widest and most nearly horizontal area. This area is important as it provides the most effective and balanced traction. The ratio between the pitch diameter of the top and bottom rolls must be the same as the ratio of the gearing connecting the top and bottom spindles.
Some manufacturers provide machines that are able to accommodate either equal ratio or unequal ratio rolls. On the left of Figure #2 is a cross-section through a stage of equal pitch diameter rolls. The drawing on the right shows the same roll stage in a machine fitted out for unequal ratio rolls. The pitch diameter in the latter is well below the mid-point between spindles and as you see, gains enough space to allow forming a much deeper section with the same vertical centers.
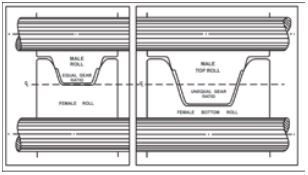
In machines where only equal ratio rolls can be applied, deep sections are formed by “floating
the pitch line.” This is not a good procedure but can be applied in specific instances, particularly where light gauge and perhaps narrow shapes are concerned. In principle, it
involves a different pitch diameter in successive roll passes which, as each bottom spindle is driven at the same rpm, can lead to “roll fight” between passes, excessive gear loads and excessive horsepower demands.
In summary, beyond the number of roll forming stations available, it is important to consider the available vertical distance between spindles, as well as the gear ratio. The combination of vertical spindle distance and gear ratio will define the maximum height of the finished profile that can be formed. If you are concerned about sizing the products to fit in your existing roll forming machine, or want help in sizing a new machine, contact your equipment supplier.