Which do you need: a straight tube or a pre-stressed tube?
Our answer to that question is another question: why not both?
That's right - both can be accomplished with straighteners.
The tube, pipe and wire industries all utilize straighteners both in-line and off-line with regard to the main manufacturing process. Straightening these products involve “stressing” the tube in a particular plane(s) to counter-act forming, internal material, or welding heat stresses. All of which can be removed or balanced by using straighteners.
There are many types of straighteners used in today’s manufacturing environment: multi-roll or multi-plane, Turkshead, and cross-roll. Cross-roll straighteners tend to be used as an off-line processing action, since the tube or pipe is typically cut to a finite length and the tube or pipe is rolling radially as it is processed. Turkshead straighteners are used on tube and pipe mills in-line and use either 2 or 4 roll designs to encompass the tube and impart a force (or stress) in up to 2-axis of direction.
Multi-roll or multi-plane straighteners tend to be used to counteract forces within a tube, pipe or wire that are variable and multi-direction as the product moves through the straightener.
Turkshead straighteners involve an operator to adjust the unit to counteract the internal stresses, but as these stresses change, the Turkshead must also be changed. This is not entirely true with a multi-roll or multi-plane straightener. This unit is more robust to small changes as it stresses the tube multiple times to achieve straightness. In essence, you “beat” the product up to achieve your desired goals. More rolls can be added to reach a point where an operator is not required for all but the most stubborn material characteristics.
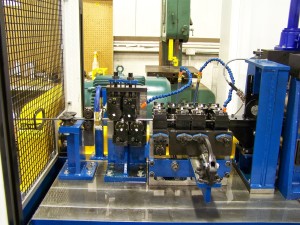