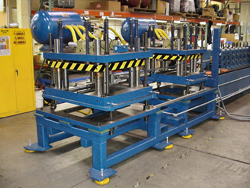
The reason we can produce the punching at these high speeds and accurately is due to the servo technology operating as follows. A rotary hole punching machine's encoder tracks the speed of the material along with lineal inches passing under the roll and sends this information to the servo. The servo then rotates the rotary puncher through a precision gear box to match the material speed at the proper punching position in the strip and continues around to a home position.
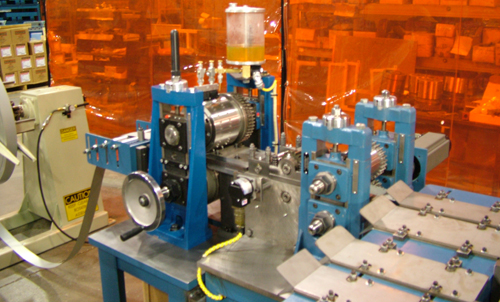
The rotary action provides punching in a smooth motion, continuously rotating in one direction, not like the pounding impact of the linear motion back and forth when using an air press or hydraulic system. Keep in mind that we build linear motion air and hydraulic systems too and not just for Stud lines but for all types of markets and products; however, for high speed punching we go with rotary action whenever it is realistic to do so.
If it is high roll forming line speed you need in order to compete, then you might as well get one that is capable of running your full product range with all the required patterns. There is no reason to slow the line down when punching on only 2 foot centers, such as is necessary when running a line with a post-punch flying die system.
In order to get even close to this speed with a flying punching die, the punching system must operate with an “open loop” measuring unit so it can hit, return and make another hit as quickly as possible. Therefore, the line speed is not only slower to hit a 2 foot or even a 4 foot pattern but to achieve the speeds, the hole centers are not accurately positioned because an open loop system measuring system is relying on precision repetitive timing and valve operation and not the precision tracking and speed matching of a closed loop servo driven measuring/accelerating system.
By the way, the rotary punch and die components are mounted in quick-change cartridges for rapid and accurate change-over to punch different sizes of openings.
We have found that combining the rotary hole punching machine technology with a servo-driven rotary pre-shear makes this the most efficient type of line available for running Stud and Track at 500+ fpm consistently, day in and day out.