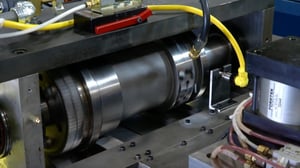
Hill Engineering/Formtek Inc. has designed and built both rotary punching machine systems and flying die machine systems in roll forming machine lines for over 60 years. From this extensive experience we have found that the most efficient way of running a high speed stud line with the option of punching both 2 foot and 4 foot centers at the full line capability of 500 fpm is to rotary pre-punch and rotary pre-shear using servo-drive technology.
If this is the roll forming line speed you need in order to compete, then you might as well get one that is capable of running your full product range. There is no reason to slow the line down when punching on only 2 foot centers, such as is necessary when running a line with a post-punch flying die system.In order to get even close to this speed with a flying punching die, the punching system must operate with an “open loop” measuring unit so it can hit, return and make another hit as quickly as possible. Therefore, the line speed is not only slower but to achieve the speeds the hole centers are not accurately positioned because it is not a closed loop tracking servo driven measuring/accelerating system.
By the way, the rotary punch and die components are mounted in quick-change cartridges for rapid and accurate change-over to punch different sizes of openings.
The rotary pre-shear is designed to cut off the widest blank to make your widest stud. Therefore, there is no change-over time required for the cutoff when changing the stud width such as is necessary when using a flying post-cutoff die!
Also, when pre-shearing while running Stud and Track, the roll former machine incorporates side angle pass (SAP) roll stations near the end of the roll former machine to make sure the side walls are square to the base. This makes sure that you achieve industry standard product coming out of the roll former.
Pre-punching and pre-shearing is not the problem that some OEM roll form equipment builders imply that it is. These lines, when designed and built with state-of–the-art high speed rotary punching technology and quick change capability, can’t be equaled for high speed operation and rapid changeover.
This the most efficient type of process available for running Stud at 500+ fpm consistently, day in and day out.