The performance of the roll former and the tube mill have been revolutionized by the rapid progress of laser mill alignment technology in recent years.
It wasn’t long ago that machine tool calibration and alignment methods required an indefinite number of days, even weeks, to complete. Not anymore, not with a laser. Furthermore, the lifetime of the equipment has vastly improved and the final products are of much higher quality.
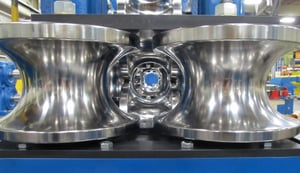
At Formtek, we have developed programs to take advantage of these breakthroughs, beginning with a team of highly-trained laser alignment technicians. Applying their skills, it now takes approximately one day to laser align a typical shop, both in new installations and existing mills.
For new mills, when the Formtek Service team is verifying the installation of the machinery, the latest laser alignment technology can be employed to check the machinery position is correct, as it was set up at the Formtek factory, before shipment to the Customer. Complete testing and verification of all system components are carried out, and in-house training provided at the same time.
For existing mills, the Formtek team also handles all the major procedures, including identifying and correcting alignment anomalies. On a roll forming machine, these could include, for example, double tracking of radii (likely related to improper tooling setup), severe scuffing, and an excessive amount of bow caused by stress.
Any of these anomalies could easily affect the extremely close tolerances that are essential for roll former and tube mill alignment. For example, the maximum end play for a mill drive top shaft is 1/32” and just 1/64” for the bottom shaft.
Today’s laser mill alignment technology certainly goes a long way in maintaining the needed tolerances for keeping roll formers and tube mills operating at maximum efficiency. This proficiency allows for significant business flexibility when responding to economy upturns and downturns, while also ensuring high quality for the finished products.