In this post, we will discuss techniques for improving the line speed and efficiency of production lines with various types of dies.
Methods to Reduce Die Sliding Friction 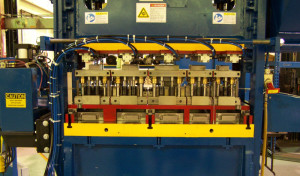
Fighting the resistance to sliding is one of the big problems constantly faced when building “flying” dies. Anything that can be done to lessen the resistance to movement of the die will increase the line speed.
With light dies, linear roller bearings and shafting can be used. Instead of the die riding on slides mounted to the bolster plate, linear bearings are attached to the die. These bearings ride over hardened shafting mounted to the bolster plate.
A method used to lessen friction on medium-sized die cutting on high-speed lines, where rapid acceleration is necessary, is to let the die roll on a series of rollers trapped in a cage.
The method used to reduce friction on large dies or on dies that require much tonnage to cut off is a receding roller bearing.
Press Requirements for Accurate Length
Another subject which cannot be left out when talking about dies is the punch press.
There are two important things to look for in a press for a cut-off die:
- The RPM of the press--the faster the better.
- The consistency of the top stopping point (or rest position) of the ram.
The RPM are important when considering that there is always some fluctuation in line speed. A 300-RPM press will show only 1/3 of the error that a 100-RPM press will show when we get a line speed fluctuation.
The consistency of the top stopping point of the ram is very important and affects the length accuracy whether the line speed fluctuates or not.
It goes without saying that the faster the press is, the less linear die travel we get. Therefore, for an additional investment to get a faster press, a person can probably run a roll forming line faster, with fewer problems, and better length tolerances, for the life of the line.
Economics of Using the Correct Dies and Systems
There is a close, direct relationship of the engineering on a line to the economic payback of that line. By picking wrong methods or systems, you will make the line less profitable by operating too slowly. The line could need too much maintenance, or require expensive secondary operations. You could also tie up a line, which potentially could be used for running additional products.
I look at it from the standpoint of the roll forming line as a whole being an immense investment. Why not, since there must be a cutoff press anyway, make it the right one? Why not, since you must pay for a cutoff die anyway, make it the right one? Sometimes it does not cost more to do it right.
Why run the risk of an expensive line being down or operating at a low return on investment? Investing more time and/or a little more money in the proper auxiliary tooling can prevent this issue.
Companies that change their production lines from press braking to roll forming are lulled into complacency by the great improvement in production times. Once you switch to form rolling, you should no longer continue to compare the production you are getting what you used to get. You should look critically at your roll forming production methods. It's always possible that you could refine your line to be even more efficient.
As more competitors turn to roll forming, the differences that will keep one company ahead of the others are in the better engineering of auxiliary roll forming tooling and improved total system engineering.