The fabrication and metal manufacturing world can be difficult to understand if you're not a veteran on shop floor. Not only that, but when you want to look something up, clear explanations can be hard to come by. That's why we're starting up a blog series on metal forming terminology - a handy ABC dictionary for any metal forming professional to refer to. Whether you're looking for answers or testing your knowledge, find the answers here!
Materials
- ASTM - Stands for "American Society for Testing and Materials"
- Cold rolled sheet - A product manufactured from hot rolled, descaled (see "Pickling") coils by cold reducing to the desired thickness, generally followed by annealing and temper rolling. If the sheet is not annealed after cold reduction, it is known as "full hard."
- Corrugated metal - Metallic coated sheet steel formed to a finished shape by passing the metal sheet through an engineered set of rollers by a metal fabricator.
- Corrugating -
- a) The process of forming or ribbing a flat sheet of material into a consistent, symmetrical profile to increase that material's strength to weight ratio up to 30% over the conventional material.
- b) The forming of sheet metal into a series of straight, parallel alternate ridges and grooves with a rolling mill equipped with matched roller dies or a press brake equipped with specially shaped punch and die.
- Corrugations - Transverse ripples caused by a variation in strip shape during hot or cold reduction.
- Ductility - The ability of a material to be bent or otherwise formed without fracture. This is very critical in the roll forming process.
- Elastic Limit - The maximum stress that a material will stand before permanent deformation occurs.
- Ferrous metals - Metals which are iron-based.
- Form -
- a) A bend in a material.
- b) The process of bending a metalformed part.
- Galvannealed - Steel sheet that is covered with zinc on both sides and immediately heat-treated so the coating becomes a zinc-iron alloy bonded to the surface.
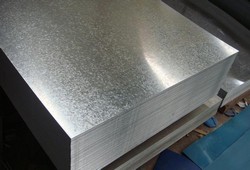
- Hard-rolled Steel - Steel that was formed by rollers from a hot plastic state into its final shape. It is characterized by a rough, scaly surface.
- Load capacity - Material type and thickness establish the load capacity that a given roll forming machine is required to generate.
- Non-ferrous metal - Metals or metal alloys that do not contain any iron.
- Pickling - Pickling, or descaling, is the name given to the process of cleaning steel coil through a series of hydrochloric acid baths that remove the oxides (rust), dirt, and oil so that further work, such as roll forming, can be done to the metal.
- Prototype - The first part of a design which is made to test tolerance capability, tooling concepts, and manufacturability of the intended production part.
- Roll forming metals - The roll forming process can handle a wide variety of metals including ferrous, nonferrous, hot rolled, cold rolled, polished, plated, and pre-painted metals.
- Sheet - A wide but thin (down to 0.05") flat rolled metal mass typically provided in widths from 24" to 80". It can be sold either in cut-to-length pieces or rolled into large, heavy coils.
- Stainless steel - Corrosion resistant steel of a wide variety, but always containing a high percentage of chromium. These steels are highly resistant to corrosion attack by organic acids, weak mineral acids, atmospheric oxidation, and other corroding materials.
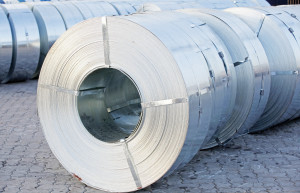
- Steel - Iron, malleable in at least one range of temperature below its melting point without special heat treatment substantially free from slag, and containing carbon more than about 0.05% and less than about 2.00%. Other alloying elements may be present in significant quantities, but all steels contain at least small amounts of manganese, silicon, and, usually as undesirable constituents, sulfur and phosphorous.
- Thickness - The gauge or depth of a material.
- Yield Strength - The maximum stress that can be applied to a material without permanent deformation of that material.
Tags:
Metal Forming