Whether you're considering getting started with roll forming or expanding your capabilities with a new machine, it's important to consider the value of your investment. Roll forming can significantly increase your productivity and the quality of your finished products when you make an educated decision based on your shop's unique needs. In this post, we'll discuss the value of a roll forming line in terms of cost, production rate, and operation controls to help you decide if or when roll forming is right for you.
Machine Cost and Life
The initial cost of a standardized roll forming line with a coil reel, cutoff, and electrical equipment, ranges from about $100,000 minimum up to $500,000 or more, depending on the size and number of roll stands. The median would probably lie somewhere between $150,000 to $250,000 without tooling. There is practically no limit to the life of these machines; maintenance, including replacements, is small or negligible even in a very old machine so long as it is not being abused. The obsolescence factor during the part decade or so, has also been very small. Although machines have been constantly improved in accuracy, accessibility, ease of adjustment and wearing qualities, the basic design has not been changed.
Production Rate and Conversion Cost
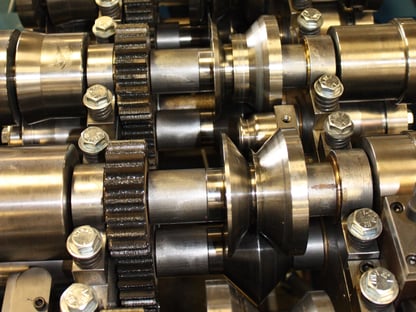
Standard roll forming machines are usually equipped for operation at a nominal rate of 100 FPM, but may easily be designed for a higher or lower speed to meet a specific requirement. At this rate, daily production averages about 25,000 to 30,000 feet of section of 8 hours taking into account the usual delays for loading coils, threading the mill, clearing away finished product, and those other elements of downtime that might enter the picture.
Conversion costs obviously vary from plant to plant and from one requirement to another. For this reason a general observation becomes almost meaningless; each job must be analyzed individually. But, the high productivity and the low operating expenses involved provide a break-even point invariably so low one can conclude, if roll forming can be used in shaping any product, the conversion cost will be lower than obtainable with any other method. With today’s electrical controls and computer technology, it is possible to integrate the roll former operation with a business’s MRP system to schedule when and how much product is roll formed.
Lengths, quantities, and hole patterns can be directed from a companies incoming orders and routed to the roll forming machine controls, with the inclusion of product specific labeling or inkjet marking to identify the product coming off the roll former to the order for which it was made. Such integration can be added on existing roll former installations with the upgrade of some controls, or planned in the early stages for new installations. Also, in order to operate such a system, it is necessary for the facilities to have the hardware and software infrastructure to manipulate incoming orders to a data format that can be processed and transmitted to the roll formers production queue.
Production Management and Operation
With today’s electrical controls and computer technology, it is possible to integrate the roll former operation with a business’s MRP system to schedule when and how much product is roll formed. Lengths, quantities, and hole patterns can be directed from a companies incoming orders and routed to the roll forming machine controls, with the inclusion of product specific labeling or inkjet marking to identify the product coming off the roll former to the order for which it was made. Such integration can be added on existing roll former installations with the upgrade of some controls, or planned in the early stages for new installations. Also, in order to operate such a system, it is necessary for the facilities to have the hardware and software infrastructure to manipulate incoming orders to a data format that can be processed and transmitted to the roll formers production queue.